「無茶振り」こそ自分を高めるチャンス──変革の中心に身を置き、がむしゃらに楽しむ極意を聞く
Sponsored非連続、 想定外。これらにうまく対応するのがビジネスといえるのだが、それにしても、新型コロナウイルスの感染拡大により、2020年は史上まれに見る想定外の連続だったといえるだろう。多くの企業で、事業の進め方が変わり、その対応に追われ続けているビジネスパーソンも少なくないはず。
そこで紹介したいのが、あの歴史ある大企業、日本たばこ産業(以下、JT)における数年前の変革だ。あるイノベーションにより、事業環境が大きく変わり、仕事の進め方を大きく変えることを余儀なくされた。そんな日々について聞く機会を得た。
「新しい価値は、当たり前だと思っていた考え方の枠外からやってくる。変化の中に身を置いた当初は楽しくないと感じることもあったが、どんな環境にも恐れず飛び込む経験を積んでいると、変化が楽しめるようになる」。言葉の主は、JTにおいて国内外を渡り歩いてきた西出一大氏だ。
海外経験も豊富な西出氏が「どんな想定外や無茶振りよりも厳しかった」と語る、加熱式たばこの製造体制構築ミッション。これが今回の記事の主題だ。多岐にわたる業務を経験してきた西出氏にそこまで言わせるこの変革、難しさはどのようなものだったのか。そして、そこから得られた逞しさもにじみ出るインタビューを、ここにまとめた。コロナ禍での変革にも、ヒントが得られるかもしれない。
- TEXT BY YUKI KAMINUMA
- PHOTO BY SHINICHIRO FUJITA
国内外のたばこ製造を担う製造グループ
このインタビューの本旨は、JTが「RRP(Reduced-Risk Products、リスク低減製品*)」と呼んでいる、いわゆる加熱式たばこなどの製品の導入という大変革により、製造現場がいかに大変な苦労を乗り越えたのか、というものだが、そもそもたばこの製造について知っているという読者はごくわずかだろう。
(*……喫煙に伴う健康リスクを低減させる可能性のある製品)
工場で製造されるたばこの多くは、たばこの葉に商品ごとの味や風味付けをして、すぐに吸える形に包装する、といった流れで生産されている。JTの「製造グループ」が紙巻たばこや加熱式たばこなど様々な形態のたばこ製品の製造を担っており、国内で5つの工場を有する。また、JTグループの中で海外たばこ事業を担うJTI(JT International)は、世界28か国で35の工場を有している(2019年末時点)。
製造業に関わりがある読者なら、「Quality(品質)」「Cost(コスト)」「Delivery(納期)」という言葉を聞いたことがあるかもしれないが、この3つをいかにバランスよく、高次元に高めるかを追求することが、製造グループのミッションだ。西出氏も、JTの製造グループでキャリアを歩んできた。
前例も前提もない経験で「逞しさ」を培ったキャリア
たばこ製造ど真ん中の人物が登場すると聞いていたのだが、JTに入社する動機は意外なものだった。
西出実は就職活動時には、食品部門で飲料事業をやりたくて、JTの選考を受けていたんです。当時、『桃の天然水』とかが売れていた時期で、「いろいろなことをやっていて、新規事業も多そうで面白そう」というイメージを持っていました。
結局、飲料は一切やることなく、たばこ事業一筋で約20年ほどになるんですけどね(笑)。ちなみに私は、たばこ吸わないんですよ。
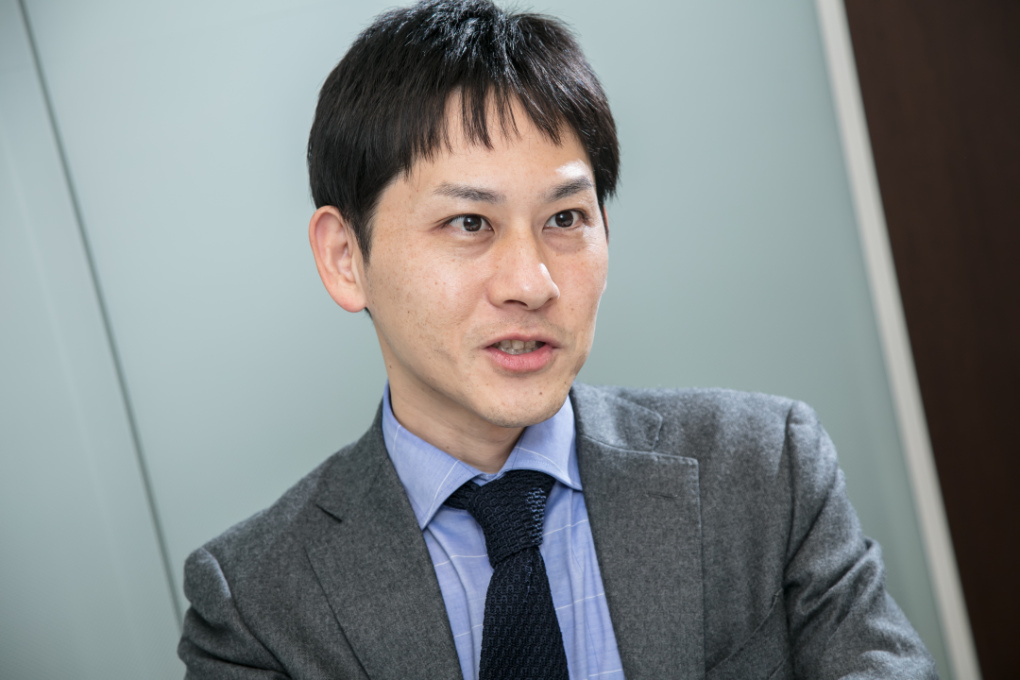
このように入社時はたばこ事業にはそれほどに興味もなかったと打ち明けた西出氏。だが非喫煙者でありながら、その入社から約20年後、大きな変革となった加熱式たばこ導入に伴う、製造現場の大転換を牽引したのだという。
入社直後は浜松工場に配属になり、製品製造工程・生産管理などを経験。たばこ作りの基礎を学んだ。その後本社に移り、中長期を見据えた製造グループの経営計画策定や、エンジニアリングの観点から研究開発・製造・マーケティングの架け橋となる業務などを幅広く担当した後、2014年にドイツにあるJTIトリアーに赴任した。
話が逸れていってしまうため割愛するが、海外勤務でのさまざまな挑戦を通してたくましさを身に着けた。未進出の国でマーケットを開拓したり、工場の無い国に工場を立てたりなど、前例も前提もない仕事に向き合う日々。「日本ではとても想像できないような事態に見舞われることも珍しくなかった」と苦笑いして振り返る。
そうして約3年の時を経て、今回のインタビューの舞台となる国内を代表する製造拠点である東海工場でのプロジェクトにアサインされた。
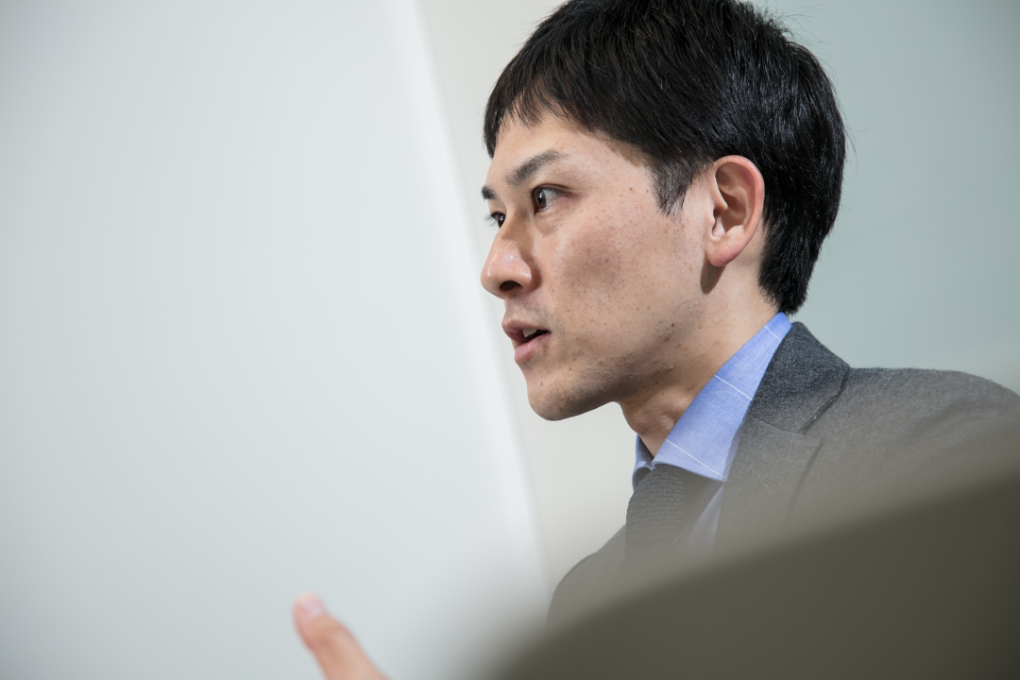
「これまでの経験が全く活きなかったくらいキツかった」という、2017年4月に飛び込んだ、加熱式たばこ『Ploom TECH』製造体制構築プロジェクトだ。
知見は現場で拾うしかない、前代未聞の変革プロジェクト
従来のたばこ製造機械といえば、もちろんすべてが紙巻たばこ専用だ。工場では紙巻専門のエンジニアやオペレーターを配置し、製造体制も紙巻に特化している。開発、調達、製造まですべてのプロセスが、紙巻たばこのために出来上がっていた。
紙巻たばこと、加熱式たばこでは、その形状も原料も大きく異なる。紙巻は、刻んだたばこの葉とフィルターを、文字通りに紙で巻いてつくる。一方、JTがつくる加熱式たばこは、葉をさらに細かく粉砕し、プラスチックのカプセルに詰めたものになっている。
そんな加熱式たばこの本格的な製造体制構築が社を挙げた至上命題となったのが2016年ごろ。最初はマイノリティだった加熱式たばこのマーケットが急速に拡大し、JTも早急に量産体制を整えていく必要性が生まれたのだ。製造グループのメンバーの、ひたすら走り回る日々が始まった。
2017年、西出氏は海外勤務から呼び戻され、東海工場へと配属された。ここはJTのたばこ銘柄数を最も多く製造する工場。紙巻たばこのピース、ホープ、メビウスといった銘柄を製造してきた。つまり歴史ある紙巻たばこの製造工場だ。 Ploom TECH製造機械導入と量産体制構築のプロジェクトは、この東海工場で始まったのである。
西出海外から呼び戻されたものの、詳しいことは知らされていませんでした。もちろん、ついにJTが加熱式たばこというチャレンジを始めた、というのは聞いていましたが、それがどれだけ大変なことなのか、全く見当がついていませんでしたね。
Ploom TECHの製造工程は、同じたばこであっても、紙巻と全く異なるものだった。例えば、原料となるたばこ葉を、紙巻の場合よりも非常に細かく粉上に加工する。そこに、香りのもととなる材料を加え、紙で巻くのではなくカプセルに充填し、ブリスターというプラスチック包装で製品としてまとめ上げる。
西出初めて東海工場に足を踏み入れたとき、ちょうど開発初期の低速で稼働する機械がありました。でも、何をどうやって作っているのか、イメージが全く湧かなかったのです。 なので急いで、別の機械を担当していたメンバーと一緒に、製造機械の出荷検査を見に行かせてもらいました。そのサプライヤーの現場で、機械の内側や裏側まで見て、「これはもう、たばこ製造の機械じゃない」と思いました。
「どうやら、頭のなかにある、紙巻たばこのイメージは一旦、忘れないといけないようだ」と。これまでの仕事とは全く異なる、大変なプロジェクトだなということに気が付いたんです。
西出氏が担ったのは、製造本格化に不可欠な高速製造機械の工場への導入と立ち上げ。市場に商品を継続的に出していくための製造ラインを作り上げるため、想定する体制に必要となる大量製造が可能な機械を、イタリアの機械サプライヤーから導入した。それは先述の低速の機械を大きく進化させ、高速で製品を製造するラインを立て続けに工場へ導入するというミッションだった。
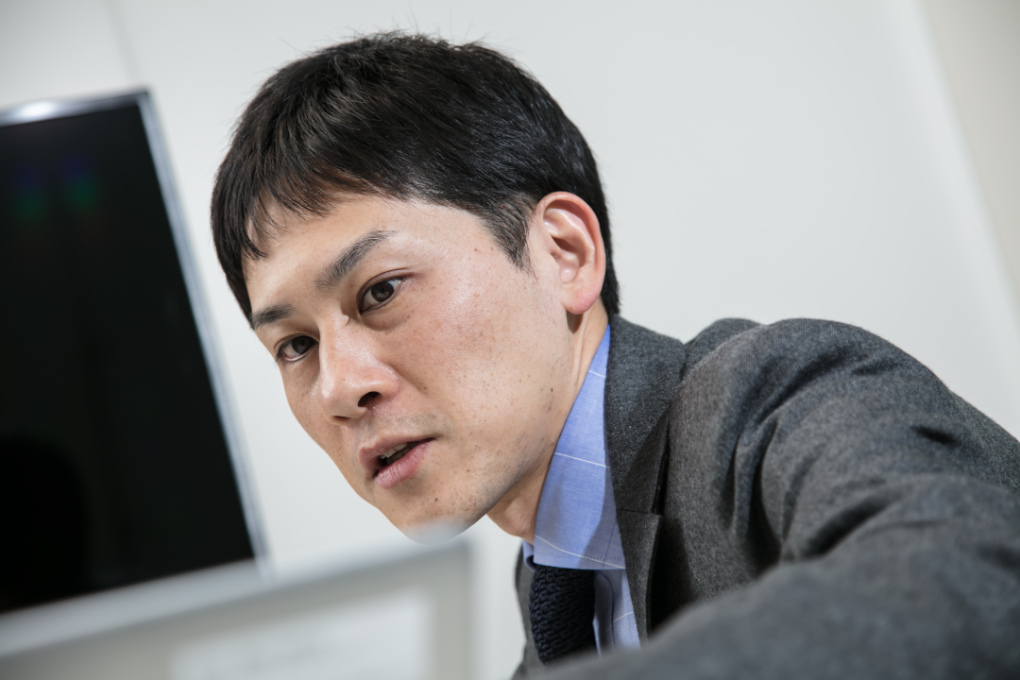
東海工場における製造体制本格化に向けての、いわば最重要任務を担ったような形だ。だが、海外でゼロから工場を立ち上げ市場を開拓してきた西出氏のこと、すぐに順応していくのだろう、と思ったのだが、前述の通り「それまでの経験なんて全く活きなかったくらいキツかった」のだという。
1人の経験はたかが知れている、メンバー総出で問題をつぶす日々
西出氏の困惑を増大させるかのように、従来の紙たばこ製造にはなかった工程が続く中でいくつもの問題が生じていった。
西出製品が違うので当たり前のことではあるのですが、製造工程で出てくる問題が全く新しいものばかりでした。問題として記録はするものの、問題として解消すべきものなのかどうかすら分からないわけです(笑)。
特に厄介だったのがブリスターというプラスチックの部材です。温度や回転数をちょっと変えただけで、プラスチックの成型紙に皺ができたり、膨らみ過ぎたりするんです。扱ったことのない機械なので、我々も工場のメンバーも、それぞれの問題にどう対応すれば分からない。輪をかけて辛かったのが、機械のサプライヤーさえ問題に対する回答を持っていないということ。なぜなら彼らにとっても初めて作る機械でしたから。
ですから、自分たちであれやこれや試しました。「温度がうまく変化していないのでは」という仮説に基づき、ビジョンで温度を感知する装置を買ってきて、工場のみんなで原因を探ってみました。「あ、ここが熱くなっている」というように、要因を一つひとつ発見していくんですよ。
私の仕事は、製品を作るために必要なものを足して、欠けているものを集め、工場として「どういう方法でモノを作れるか」という体制を整えていくことですから。
そうして知見をその場その場で、みんなで作っていくというのが面白みでした。まったくの更地から製造工程を仕上げるという、難しさや苦労でもありますけどね。
製造現場の最前線に立ち、メンバー総出で噴出する問題に向かう東海工場。「1人でできることは限られている」と、西出氏は当時の現場を振り返った。
西出特に今回のプロジェクトは、機械がない状態から始まりました。機械導入後に運転するためには訓練が必要ですが、新しい機械だから従業員が訓練するための機械もない。無理をいって、東海工場のメンバーをイタリアのサプライヤーのところに連れて行ったんですよ。その時点で使える機械で訓練させてもらったり、構造を説明したりさせてもらいました。
モノを作るのが工場の使命なのですが、このプロジェクトにおいては、とにかくモノを作る前の段階の仕事が多すぎて(笑)。
ここまで説明したように、メンバーの一人ひとりが課題意識をもって、ミッションに向き合って来たことが分かる。これまで、西出氏の力強さを伝えたが、それだけでは太刀打ちできないほどのプロジェクトだったということが少しは伝わってきただろうか。
さて、今でこそ街じゅうで見かける加熱式たばこの製品。西出氏率いるプロジェクトメンバーはこの困難を乗り越え、製造体制を確立することに成功したというわけだが、では、その終盤の苦労と、やり遂げた際の西出氏の感情とは。
100点を取れなかった悔しさと、0から1を生み出せた安堵
このプロジェクトにおける最大の困難は、JTの事業史上最も厳しいとも思われるスケジュール感だ。
たばこ製造機械の多くは、JT独自の仕様を追加して発注する。請け負うのは海外のサプライヤーばかりだ。多くの場合、紙巻たばこの既存機械なら発注から約1年で生産が始められる。すでに機械の仕様がはっきりしているからだ。ただ、仕様が存在しなければ、導入までに1年以上は確実にかかるという。例えば、先に説明したような海外の事例では、その国に存在しなかった新たな機械を導入するということになる場合がほとんどだった。
量産体制構築に向け、西出氏は一刻も早い高速機の導入と稼働開始が求められていた。
西出従来ではあり得ないほどの非常に短い期間に、新しい機械を工場にどんどん入れていくというスケジュールが引かれていたんです。既存の機械なら1年弱で導入できるのですが、今回は新しい機械なのに、なぜか1~2か月に1回のペースで導入を進めるというスピード感で計画されていました。
もちろん、ちゃんとした理由はあります。市場に製品をしっかり出していくためには、このスピーディーなスケジュールで進めるしかなかったんです。
ただ、このペースでは従来のように、「導入→運用→課題抽出→改善→新機械の最終仕様決定」というプロセスを、余裕をもって進めることができません。課題抽出と改善を常に同時並行で回していたので、文字通り頭を常に回転させていたような感じです。
このスケジュールに対して、残念ながら私の担当する高速機の完成は遅れていました。他の機械導入とは勝手が違い過ぎる、という言い訳もしたくなるほどだったのですが……。まもなく導入しなければならないというタイミングで、目指すべき能力の半分程度しか実現できていませんでした。
その時点で会社から「サプライヤーから東海工場に次の機械を出荷してください」とスケジュール通りに指示が入ったんです。私は全力で断った。
製造工場は、安定的に機械を稼働させていいモノを作りたい、製造現場がオペレーションに集中できる環境にするためには未完成の機械は受け入れるべきでない、そう考えていたからです。駄々をこねていると思われてでも全力で反対しました(笑)。
しかし「目指すべき能力の半分の状態でも製造を回せる見通しがあるならば機械を出すべき」という判断も理解できた。より全社的な視点から見れば、一日でも早くお客さんに製品を早く届けたい。
製造現場にいるからこその使命・プライドの中で葛藤があったが、そもそも東海工場に高速機を導入するプロジェクトが始まったのは、市場へのPloom TECH供給が追いついていなかったからだ。高速機が稼働しないままでは、消費者のニーズに応えられない。高速機の完成度は足りなくても、機械を導入し、とにかく生産のために全力を尽くした。
西出市場から製品を切らしてしまうのが、一番ダメなんですよね。これはメーカーとしての使命です。モノを作らない機械はただの鉄クズです。製品を出荷しないことには、製造工場としての価値がない。だから結局、高速機の完成度は足りなくてもまずは導入して、生産を急ぎました。
いざ稼働して最初の製品ナンバー「001」が段ボールに打たれた瞬間には「はあぁ~、良かった……」という安堵を感じている自分がいました。
私自身の仕事として反省も後悔も残るものの、「0」を「1」にすることができたという達成感を味わうことはできました。製造体制の構築は前進したわけです。そう捉えています。
その後も改善を重ね、新たな機械の試作も続け、少々遅れは発生したものの、2018年には目指していた製造能力を実現する機械導入を達成した。西出氏の経験と、メンバー一人ひとりの課題意識の強さで、大変革における現場の変化を推進してきたのである。
「自分の当たり前」を壊すチャンスに飛び込め
西出氏はその後、2019年よりRRPエンジニアリングセンター(インタビュー当時)に配属。RRPデバイスの技術開発に携わっている。Ploom TECHの高速機導入というプロジェクトの経験を、今後どのように活かしていきたいか尋ねた。
西出そのときそのときで、会社の環境もお客様の趣向も変わります。近年は、加熱式たばこが普及してきています。私は今後も、さまざまな変化点を楽しめる人間でありたいと思っています。変化点に対してどのくらい集中できるか、自分が食いついていけるかという意味でもありますね。
「当たり前だと思っていた考え方」というものを、誰もが持っていると思います。それはその人の枠だと思うんですけど、新しい次の世界はその枠の外からやってきます。枠外に踏み出せるような気持ちを持っていれば、どんなことにも飽きないじゃないですか。
「何これ?」と思うような環境に飛び込む機会を得るのは大事ですよね。そういった経験をしていると、次の変化が来ても「よし!」と気合が入りますし、モチベーションも上がります。
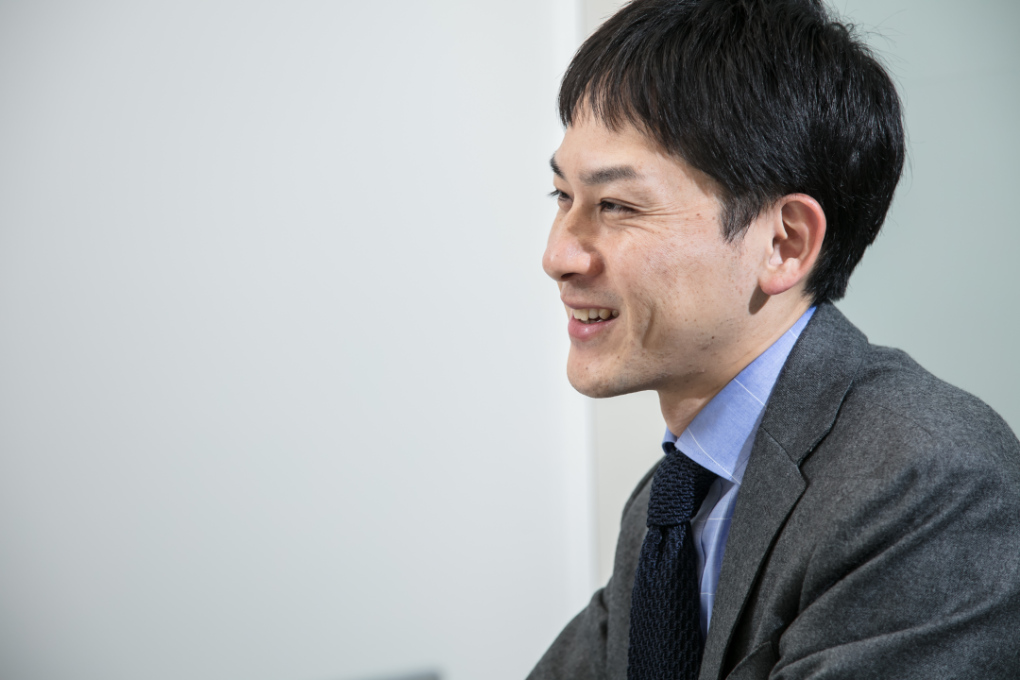
製造部として「モノを作るのが工場の使命」と明言する西出氏に、JTのような大企業だからこそ可能なモノ作りとは何か聞いた。
西出たばこを作るのにも基本がありますし、メーカーとして守らなければいけないことも絶対にあります。ただし、モノを作るという基本を守りながら、新しいチャレンジをする機会は実は多いと思うんです。大きな会社だからこそ大胆なこともできますし、それに伴う投資が発生したときには会社がきっちり判断しますから。入社前に「新しい事業とかできそう」と漠然と思っていたことも、あながち間違ってはいなかったんです(笑)。
私はそういう機会が、若い社員であろうと年配の技術者であろうと、平等にあるべきだと思っています。若い人に経験させたいというのもありますが、年配の技術者で新しいアイデアを出す方もたくさんいます。
JTは、自分の気持ち次第でいくらでもチャンスがある会社。最近の若手は海外赴任や新プロジェクトというと引いちゃう人もいますよね。でも「やってみたら面白いぞ」というのを、経験させてもらった私からもどんどん発信していきたいです。
変化を恐れず、自ら知見を生み出す。常に自分自身をアップデートすることで、社会に対して新たな価値を提供していくことができる。そんなことを教えてくれた西出氏のような、変化を楽しむ先輩と一緒に走り続けられることも、大きな魅力なのではないだろうか。
こちらの記事は2021年02月19日に公開しており、
記載されている情報が現在と異なる場合がございます。
次の記事
執筆
上沼 祐樹
KADOKAWA、ミクシィ、朝日新聞などに所属しコンテンツ制作に携わる。複業生活10年目にして大学院入学。立教大学21世紀社会デザイン研究科にて、「スポーツインライフ」を研究中。
写真
藤田 慎一郎
特別連載SENSE MAKER 変革期のたばこ産業、未来の嗜好品のかたち
7記事 | 最終更新 2021.02.26おすすめの関連記事
現場にいる者こそが、意思決定者──年次も経験も関係ない!UPSIDERで非連続成長を担うのは「一次情報を最も知る者たち」だ
- 株式会社UPSIDER 執行役員 / VP of Growth
マイベスト、実は前代未聞の“データプラットフォーム企業”だった──「あの企業の“実は”ここがすごい」Vol.2
VCも起業家も、“常識外れ”な挑戦がまだ足りない!大企業コンサルやデータ基盤提供に加え、ビルや街まで構想する「欲張り」なVC・HAKOBUNE木村・栗島の構想とは
- HAKOBUNE株式会社 Founding Partner
FinTech×EC支援で事業を連続創出できる理由とは?BASEのツーサイドプラットフォームに魅せられた山村・髙橋の躍動を追う
- BASE株式会社 上級執行役員COO
個人やスモールチームの可能性を最大限に広げるプラットフォームへ─GMV1,500億円超もまだまだ成長途上。BASEでさまざまなBizDevに挑戦できる理由とは
- BASE株式会社 BASE事業 Business Management Division Manager
2倍成長を続けるTOKIUMに学ぶ「最強のオペレーション戦略」とは──「壮大・緻密・柔軟」の3要素で、BPaaSとしての成長を実現した秘訣
勝ち筋は「国産の生成AIミドルウェア」にあり──Vol.1 miibo CEO功刀雅士氏【寄稿:DNX Ventures新田修平】
- 株式会社miibo 代表取締役